Couples Therapy for Operations and Maintenance: A Terminal Love Story
- Alon Gozlan
- Apr 17
- 3 min read
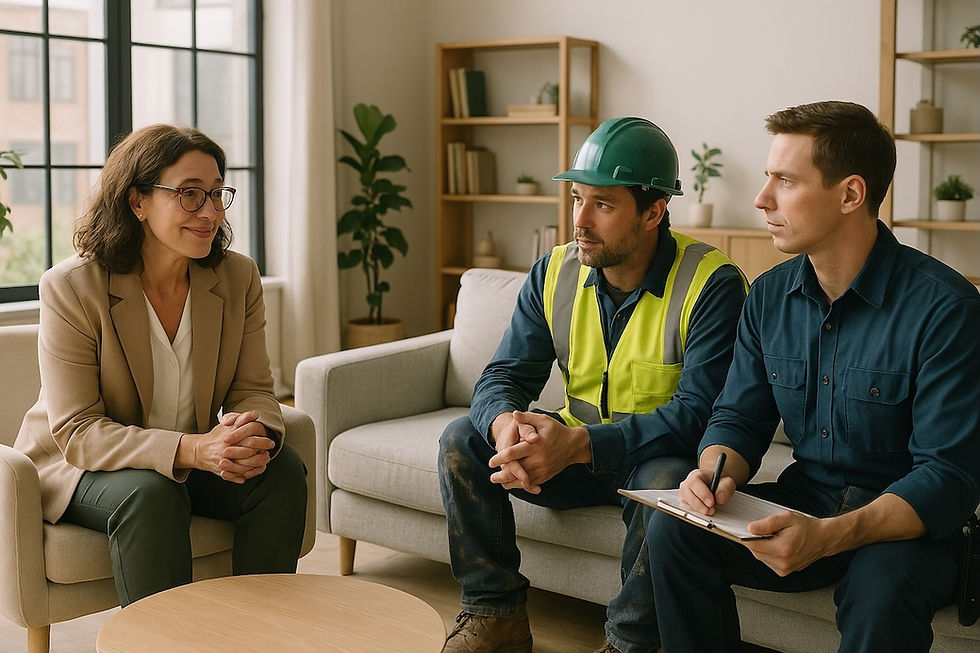
"So, tell me why you're here today," Dr. Garcia says, looking over her reading glasses at the two professionals sitting uncomfortably on her office couch.
On the left sits Operations—dressed in a high-visibility vest, work boots still dusty from the terminal, radio constantly crackling with updates.
On the right is Maintenance—clipboard in hand, meticulous in appearance, with a multi-tool poking out of a perfectly organized belt pouch.
They avoid eye contact with each other.
Session 1: Identifying the Problem
"He just doesn't understand what I'm up against," Operations starts. "Every minute a crane isn't moving containers costs us thousands. But all Maintenance wants to talk about is preventative care and scheduled downtimes!"
Maintenance sighs deeply. "And he doesn't understand that if we don't properly maintain the equipment, it won't be available at all. A stitch in time saves nine, but try explaining that when Ops is demanding we put duct tape on a critical hydraulic issue just to get through the shift."
Dr. Garcia nods. "I see this often in your industry. You're both fighting for the same resources but with different priorities."
"Exactly!" they both exclaim, then glare at each other.
Session 2: Historical Patterns
"Let's talk about what happened last month with RTG-7," Dr. Garcia suggests in their next session.
Operations winces. "Peak season, vessels stacked up, and Maintenance wanted to take our best-performing RTG offline for a three-day maintenance cycle."
"It was already 400 hours past the recommended service interval!" Maintenance counters. "The warning signs were there. But Operations insisted we keep it running."
"And it did run fine for another week," Operations points out.
"Until it catastrophically failed during the busiest shift and took out two lanes of stacking area with it," Maintenance says quietly.
"This pattern seems familiar to both of you," Dr. Garcia observes. "Short-term operational needs versus long-term equipment health."
Session 3: Finding Common Goals
"Instead of focusing on your differences, let's talk about what you both ultimately want."
"Equipment reliability," Maintenance says immediately.
"Maximum productivity," Operations answers simultaneously.
Dr. Garcia smiles. "Those aren't mutually exclusive, are they? In fact, they depend on each other."
Session 4: Communication Strategies
"Our biggest problem is the weekly planning meeting," Operations admits. "It turns into a battlefield every time."
"What if," Dr. Garcia suggests, "instead of starting with your separate plans, you began with shared data? What if you jointly reviewed equipment health metrics, operational forecasts, and historical performance patterns before making any plans?"
"That would require a system that both teams could access and trust," Maintenance muses.
"And metrics that matter to both of us," Operations adds. "Not just moves per hour for me and mean time between failures for you, but overall equipment effectiveness and risk assessment that captures both our concerns."
The Breakthrough: A New Approach
In their final session, the atmosphere is noticeably different. They sit closer on the couch, occasionally nodding at each other's points.
"We've implemented some changes," Operations reports proudly. "We've started using this platform called Opsima that gives us both visibility into what matters."
"The system helps us prioritize maintenance actions based on both equipment health AND operational impact," Maintenance agrees.
"Last week, the system flagged STS Crane 3 as needing attention. The data showed exactly how the performance was degrading and projected when it would likely fail—right in the middle of the biggest vessel call next month."
Operations jumps in. "So instead of arguing, we found a 36-hour window with lighter operations, and Maintenance was able to do the necessary work in a condensed timeframe that minimized impact."
"And because we planned it properly, the crane is now performing 12% more efficiently than before."
In port terminals, Operations and Maintenance will always have inherently different perspectives. One is measured on immediate throughput and productivity; the other on equipment longevity and reliability.
But the most successful terminals recognize that these goals are complementary, not contradictory. By creating shared visibility, aligned metrics, and collaborative planning processes, the traditional tension can transform into a powerful partnership.
After all, both teams ultimately want the same thing: a well-running terminal that efficiently moves cargo while maintaining valuable assets. It's not about whose priorities win in a given situation—it's about finding the optimal balance that serves the terminal's overall performance.